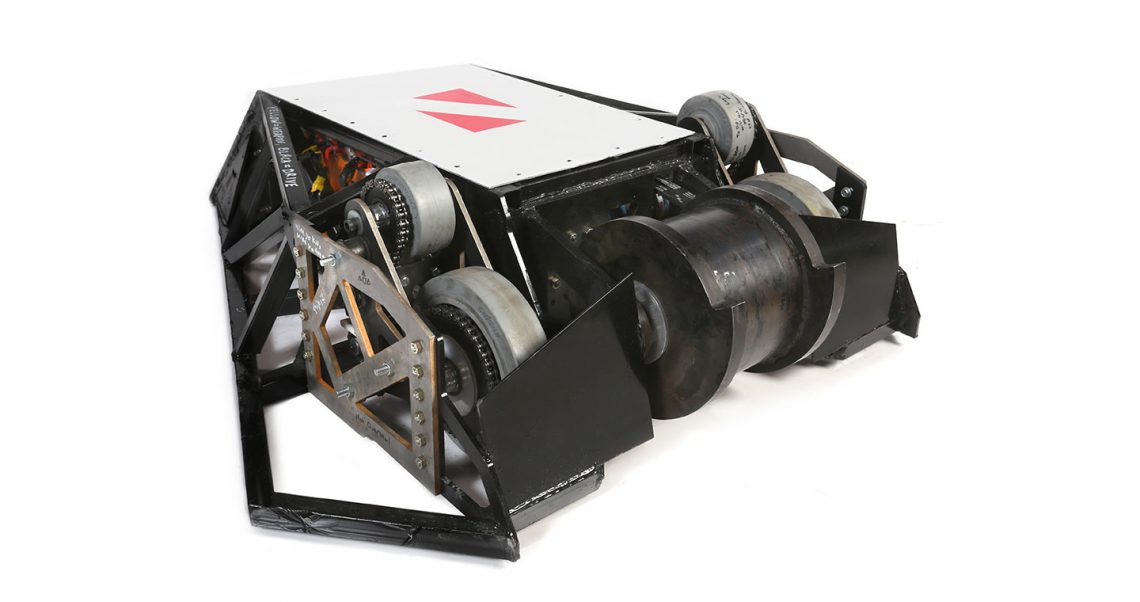
The Dentist - My Foray into combat robots, terrible timelines and extremely large extra curriculars
This is more of a reflective post, for the build report of the DENTIST, the battlebot my team built, please go here.
This past semester at MIT was a tough one for one major reason. Back in September, my friend and mentor Charles Guan, who had previously competed on BattleBots Season 1, convinced me and a gang of students to build a 250lb BattleBot for the second season. If you watched the show over the summer, of 2015 you got to see unfiltered robot destruction MMA style complete with hot announcer and burly bros. It was a good show, looked fun, and a small bit of me wanted to be on TV, which is why I decided to compete. I ended up as team captain and worked on mechanical design. The rest of the team consisted of the following MIT students: Landon Carter (CS and ME ‘17), Bayley Wang, Michael DeTienne (EE, ‘17), Daniel Gonzalez(ME, ‘14, PhD student), Austin Brown (ME, ‘18), Daniel Kramnik (EE, ‘16) Tyler Hamer (ME, ‘14, PhD Student). We built the majority of the robot in the Edgerton Center at MIT.
The inspiration for the robot was to build a traditional drum spinner for as much kinetic energy as we could muster, ideally at least 2 Tombstone’s worth, or 200kJ. For those of you who don’t watch the show, Tombstone is the traditional favorite with a dead simple spinning bar of doom. We wanted to wreck him. Furthermore, a friend of ours, Nick Kirkby, had managed to turn on a Prius Inverter and we were excited to use a Prius inverter and one of its motors in our weapon for a truly terrifying robot.
If you want the long version of on how our robot was built, you can visit the build log of it through this link. The short version is that the robot went through a ton of design changes, and we ended up building the whole thing in 12 days with a different weapon motor.. If you haven’t built robots before, 12 days is an extremely short period of time to build a robot from scratch that works. Because of that, and some motor controller issues, we ended up not competing due to safety concerns. In the end though, we did have some sort of robot, which got stripped of a lot of its armor due to being excessively overweight, which you can see below.
The Stats
- The Frame: Welded mild steel tube (1/8” to 1/16”) with a sprinkling of AR500 and titanium
- The Drive train: Two paired SK3 motors per side, powered by 150 amp DLUX motor controllers on Colson wheels
- The Weapon: A 30lb 4140/S7 steel drum powered by an EMRAX 228 motor, theoretically 200kJ of kinetic energy at full tilt. The motor controller is a Prius inverter, using the 400Amp side.
- The Battery: 220V weapon pack and a 48V drive pack (LiPo)
What I learned
I’m going to gloss over a lot of the build detailed in the build report, and even my opinion on particular parts of the bot. I do encourage you to read the build report, as it highlights a lot more technical details and learning that went on there. Here, I’ll list what I personally learned below, both about bots, TV, and large projects in general.
- Do NOT try large projects during school unless you pick a reasonable timeline and stick to it. A lot of our problems could have been avoided by having a more ambitious timeline in the beginning, and finished up a complete design. If we had a complete design earlier, we could have sent out a lot of work instead of not sleeping for a month before the competition. But in general, it’s a bad idea to not have a solid plan or your grades hurt a bit.
- SEND THINGS OUT. For the love of drill bits, there’s no reason to get DIYitis. It can be extremely satisfying to do a lot of machining by yourself (and it is in fact cheaper), but if you have the money, sending parts out is worth it. You waste less material, less time, and aren’t as worried about trying to make everything on a waterjet. Of course, this applies a lot more to people who make money and can therefore spend it, but we would have saved a lot on wasted material due to bad parts had we simply sent out for what we wanted. Your time is valuable. The only real caveat to this is as students, it is worthwhile to learn how things are made by making it yourself. You know what is easy for a shop to do and what isn’t. But once you’ve learned that it’s okay to skip the time consuming stuff if you can, and ultimately what you will be asked to do in industry.
- Having a good team is great. It really is. But teams are only good when everyone has their individual incentive to get the job done. Managing work such that everyone is working on something interesting is difficult, and something that I can definitely work on in the future. It’s also difficult to keep morale up when you scrap everyone’s work. It is important to make sure people feel appreciated as engineers (people!), not just appreciated for the things the design and build. I often wonder if this would have been remedied by having more people on the team, but also wonder if it would have led to social loafing as a penalty of large teams.
- Make prototypes. Our robot was our prototype, but if we had taken some time in the beginning to build prototypes, we would have seen many flaws in our designs before they came out in the real thing. Especially the electricals, which are easiest to bench test and cheaper to iterate.
- TV producers can actually be pretty nice, and going on TV isn’t actually a bad experience as they do take care of you. But on the other hand don’t expect them to ever portray reality or adhere to anyone’s agenda but their own.
- Steel is really heavy! Wow it’s so heavy. But it’s also really really cheap.
All in all, it was a good experience, a fun way to lead a team, and an interesting project. Would I do it again? No. While I learned a lot from this go around, combat robotics is more fun when you’re passionate about it as opposed to interested in another project. It’s fun to try to beat everyone once, but I’m ready to try a new sport for the coming year.
Tune in to the season finale this Thursday, on ABC!